The Davenport Hybrid Machine offers users precision, flexibility, and affordability in their manufacturing efforts. Simpler setups, faster cycle times, and a conventional Computer Numerical Control (CNC) interface make it easy to integrate the Davenport Hybrid Machine into virtually any workflow. This five-spindle lathes ability to hold tight tolerances with exceptional accuracy has been proven via rigorous testing.
Clients who utilize the Davenport Hybrid Machine can leverage capabilities such as:
- Cross-drilling, milling, rigid tapping, cross-tapping, profile turning, boring, single point threading etc.
- 2 & 3 axis machining capabilities
- 3 Station CNC back working axes
- Exceptional Machine Accuracy
- Aerospace alloys and other tough materials; A286, 300 Series Stainless, 400 Series Stainless, Inconel 718 etc.
Hybrid Applications
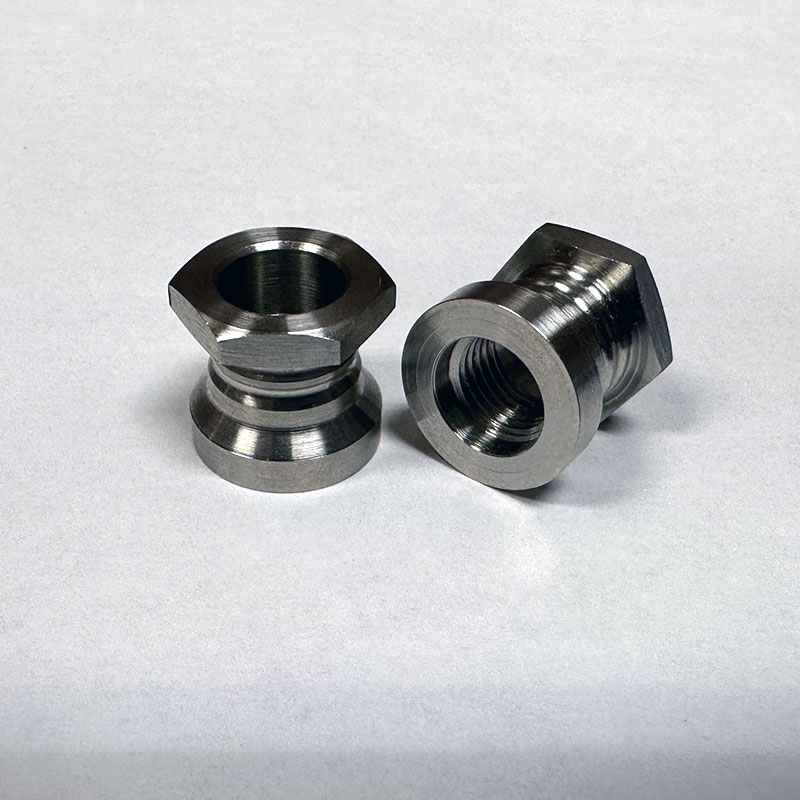
Material: A286
Cycle Time: 29s
Unique Features:
-
Tolerance Held:
±0.0005 (Form Tool)
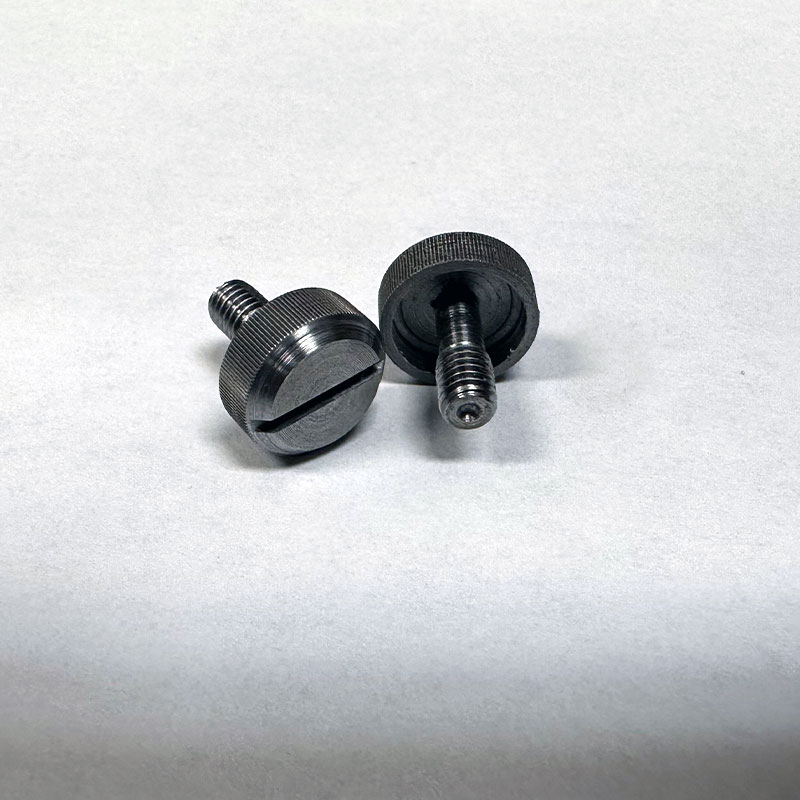
Material: 1215
Cycle Time: 6.8s
Unique Features:
- Undercut Face Groove
- Milled Slot
- Rolled Thread
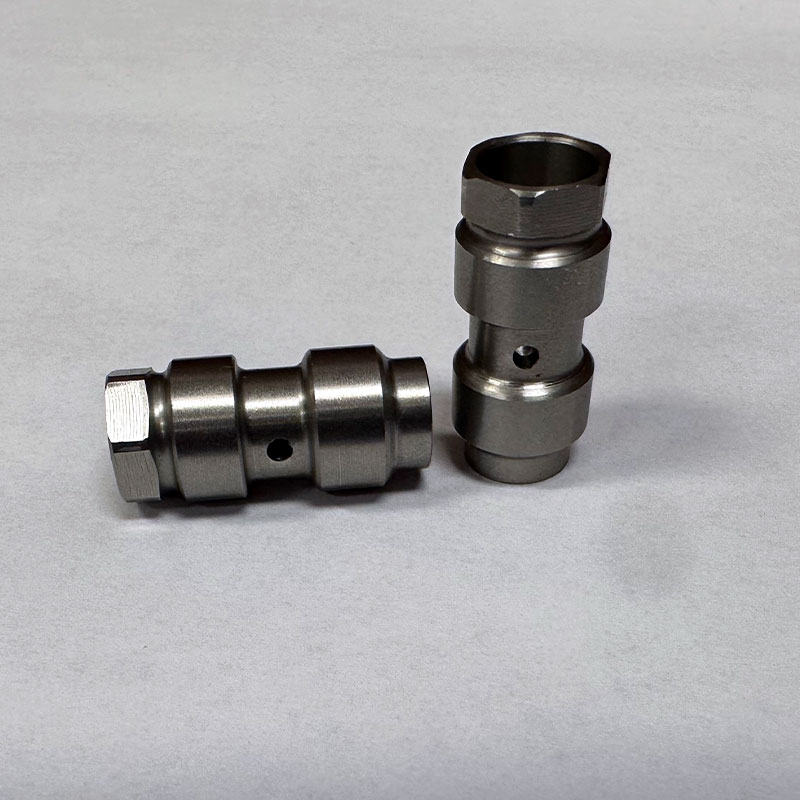
Material: 303
Unique Features:
- Contoured O.D. (+.0000 -.0005)
- Contoured I.D. with undercut
- Hex
- Cross Drilled Hole
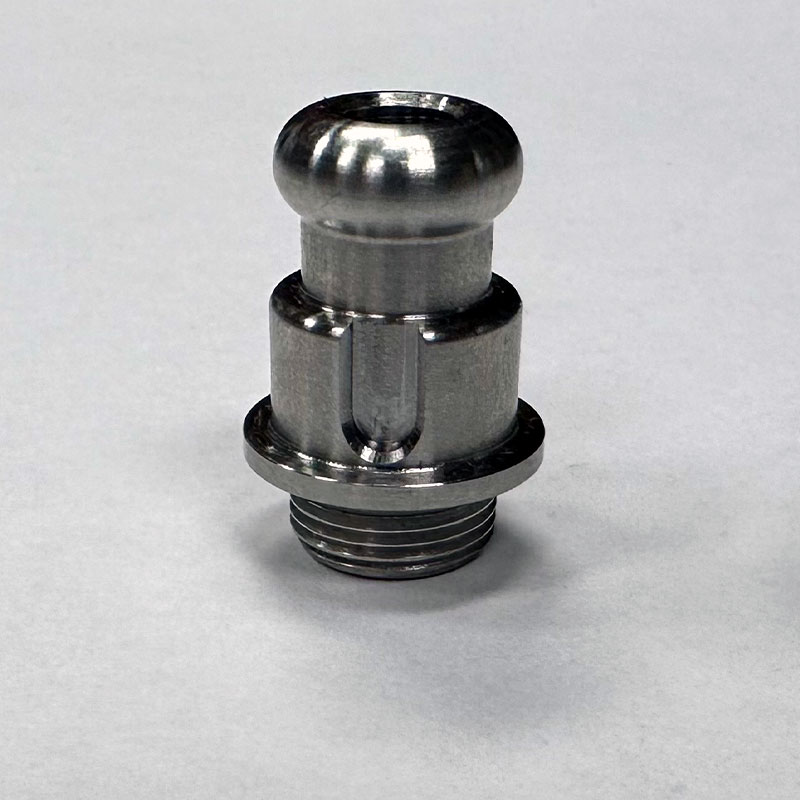
Material: 316
Cycle Time: 24s
Unique Features:
- Milled/Interpolated, Slot & Chamfer
- Single Point Thread
- Rigid Tap
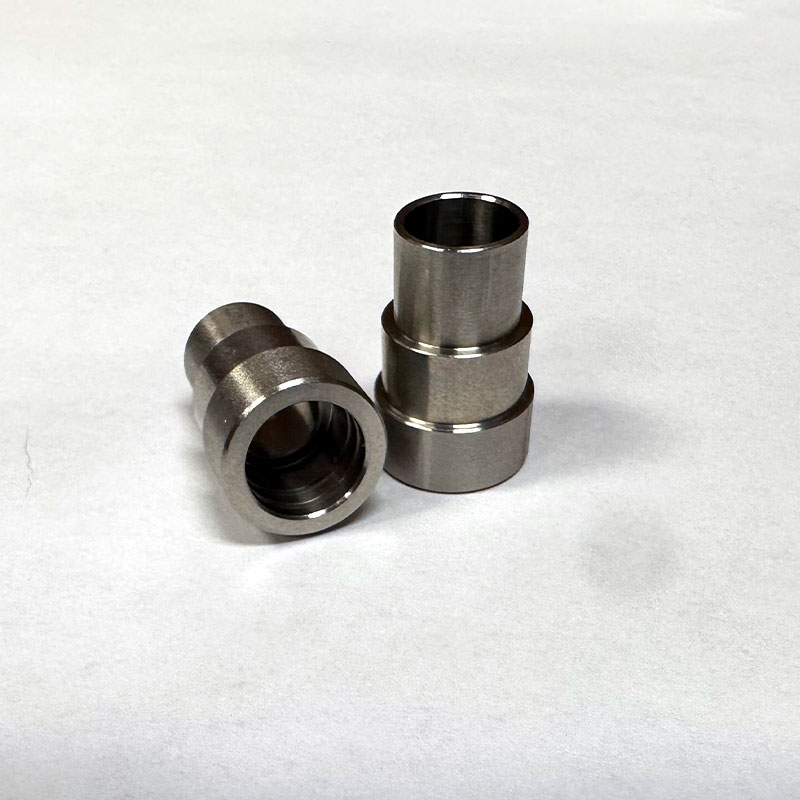
Material: 316
Cycle Time: 17s
Unique Features:
- Contoured I.D. with Grooves
- Thin walled (.030")
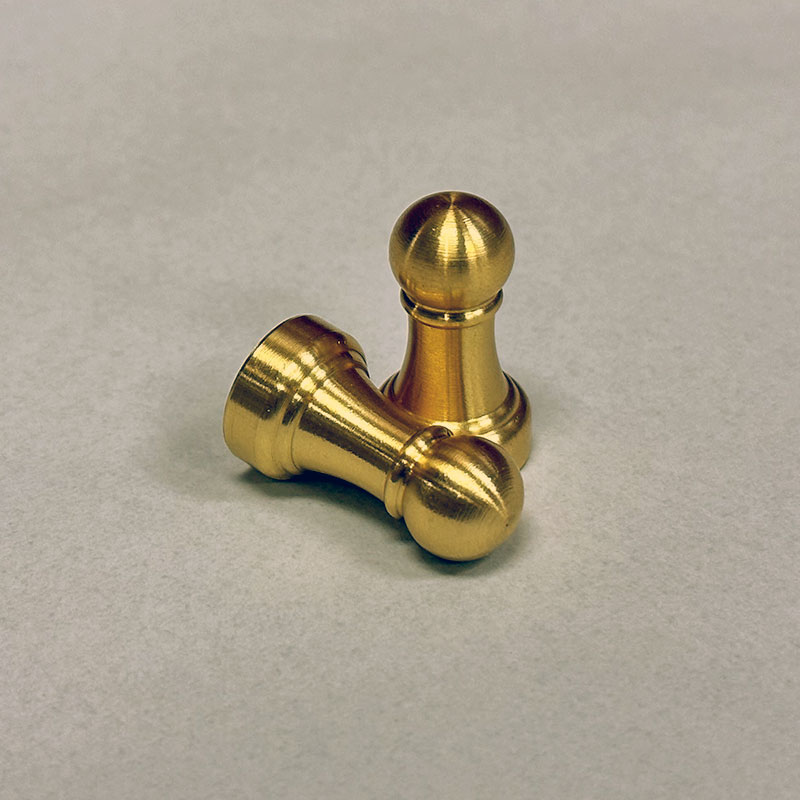
Material: 360 Brass
Cycle Time: 7s
Unique Features:
- Rough Form
- Profile Turned OD/Radii
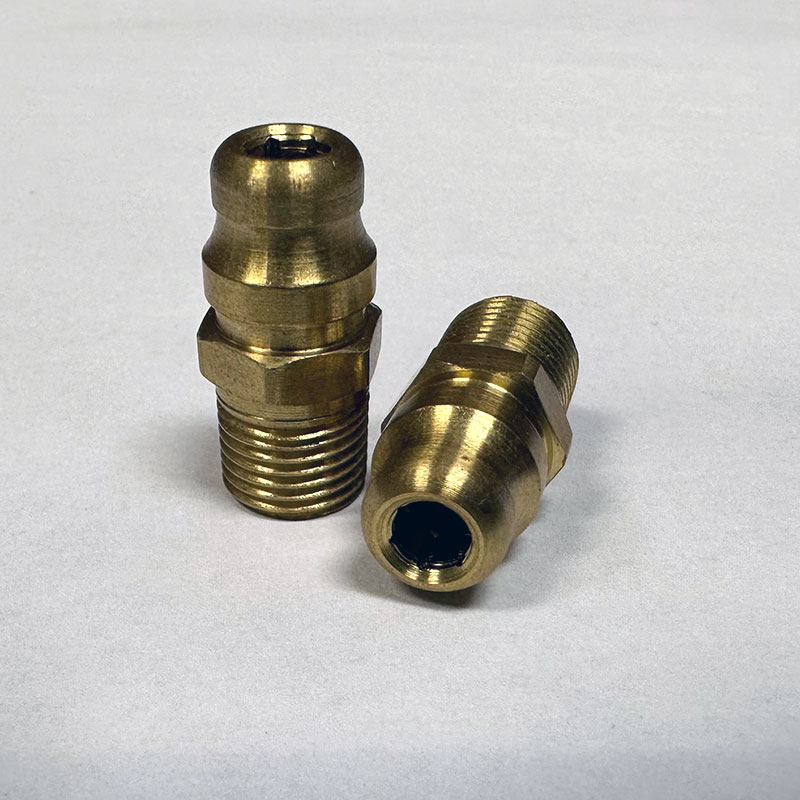
Material: 360 Brass
Cycle Time: 14s
Unique Features:
- Single point threaded 7/16-20
- Milled Exterior Hex
- Interior Hex Broach
Davenport Hybrid Machine Features
The Hybrid Machine takes the best mechanical features of Davenport’s screw machines and integrates them seamlessly with the precision provided by advanced CNC technology. Features of this multi-spindle screw machine include:
Revolving Head & Spindles on Bearings
The Hybrid Machine’s revolving head and spindles are mounted on preloaded, angular contact ball bearings. This provides exceptional accuracy and ensures consistent spindle positioning. This configuration does not require thrust ring adjustments or endplay, facilitating improved length control and reduced friction and wear. As a result, the Hybrid Machine boasts a longer than average service life.
Innovative Modular Tool System
Expanded Back Working Capabilities
The Hybrid Machine utilizes a fully CNC controlled back working axis. The back working station allows for 3 live tools to be mounted for various applications. Including, rigid tapping, single point turning or threading, drilling, spot drilling etc. The back working spindle also boasts the ability to provide 3 axis machining capabilities. Including milling and flat generation, cross-drilling etc.
CNC Cross Slides
All cross slides on the Davenport Hybrid ride on the highest quality, and most rigid linear rails and ball screws available on the market. By utilizing this technology, the Hybrid is able to consistently hold form tolerances on diameters better than 0.0005”, without the use of shave tools. The addition of 2 and 3 axis slide options in multiple positions, allow for unmatched machining flexibility and precision for cross-drilling, milling, rigid tapping, cross-tapping, profile turning, single point threading and boring operations.
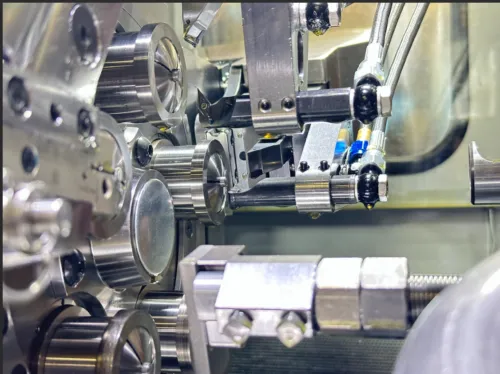
Short Indexing Time
The Hybrid Machine boasts a revolving head index time as short as 0.4 seconds. The Hybrid Machine’s expanded capabilities are not substituted for speed; the Hybrid still provides the fastest head index in the industry.
New Machine Base
Our new and improved machine base has doubled the volume of coolant that the Hybrid Machine can hold. The machine’s mass increased by approximately 25%—roughly 2000 pounds. Integrated structural supports also help improve rigidity.
Now Offering: IEMCA NEXT 25 Bar Loader
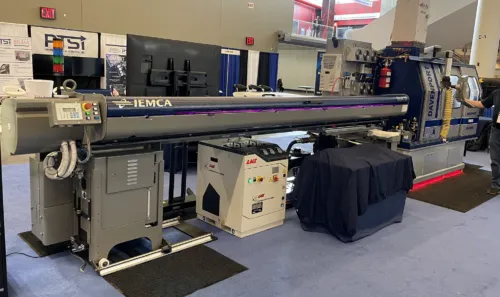
Five-Spindle Screw Machine Capabilities
Multi-spindle screw machines are a variety of turning machine. They allow manufacturers to fabricate products quickly as they utilize multiple tools to cut numerous pieces of material simultaneously. The process relies on multiple spindles carried in a precision-machined drum, which typically rotate in a horizontal orientation.
The process conducts multiple operations in each rotation of the drum and each complete rotation produces a part. This results in an exceptionally efficient process. At Davenport Machine, our multi-spindle screw machine capabilities include:
- Forming
- Back-working
- Drilling
- Reaming
- Broaching
- Cross-milling
- Flat-generation
- Cross-drilling
- Thread-rolling
- Roll Stamping
- Burnishing
- Keyway-milling
- Slotting
- Thread-milling
Partnering with Davenport for Your Machining Needs
![]() Feature Highlights |
---|
Superior Size Control |
Improved Process Capability |
Fewer Outliers |
Tighter Bell Curves |
Higher CpKs |
Lower PPM Defect Rates |
Indexing Time |
Revolving Head Index Time – As short as 0.4 secs
|
Size Capacities
|
Diameter – 7/8” (22mm) round 3/4” (19mm) Hex
|
Length – Up to 4” (101 mm)
|
Independent Spindle Size |
Each spindle can be independently, electronically adjusted for size |
“One-Touch” feature adjusts tool wear size for all spindles |
1st & 2nd Position CNC Driven Slides |
Servo driven ball screws |
Improved rigidity |
Slides on Linear Rails |
No cams or linkages |
Independent tool offsets |
Redesigned Bed Casting |
Longer work zone |
Improved Rigidity |
4th Position 2-Axis CNC Slide |
Single Point Turning |
2D Contours |
Angular Undercuts |
3-Axis Multipurpose CNC Slide |
Cross-drilling |
Milling |
Rigid tapping |
Cross-tapping |
Profile turning |
Single point threading and boring operations |
Recent Related Articles
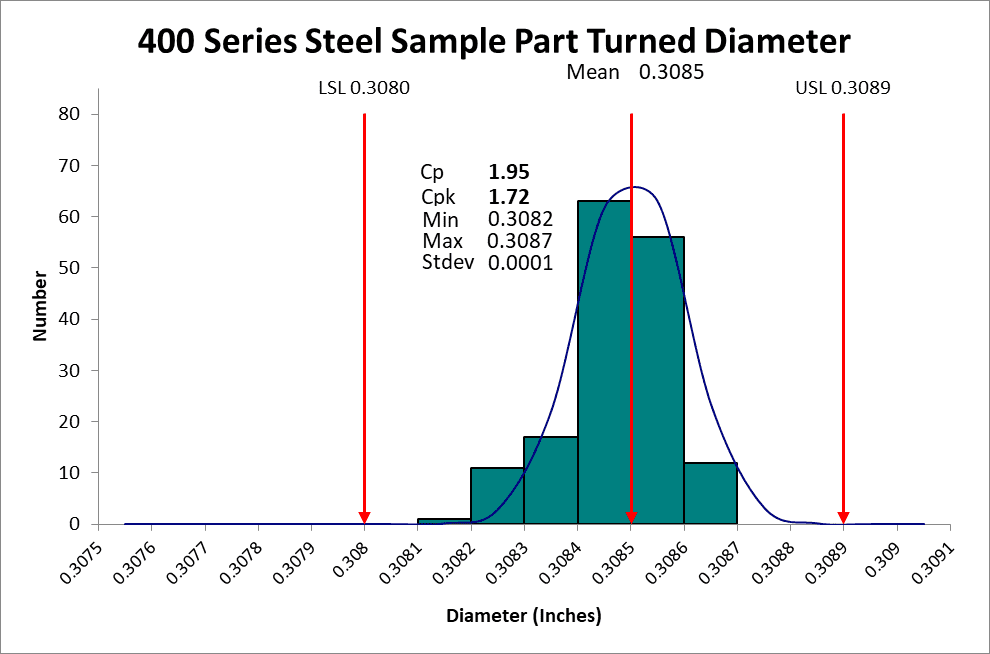
How Accurate Is A Davenport Hybrid Machine In Action?
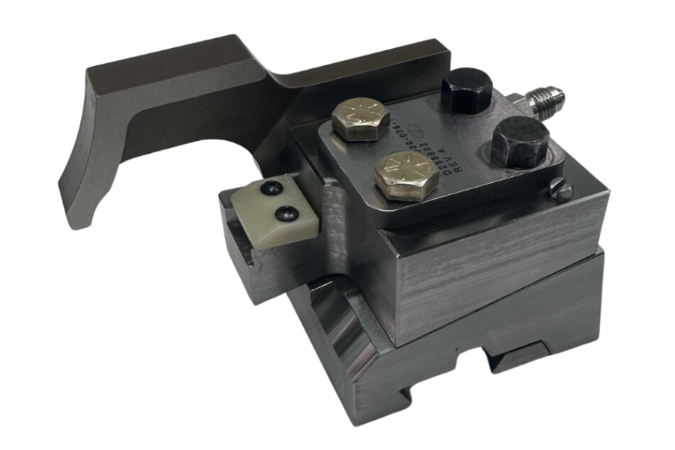